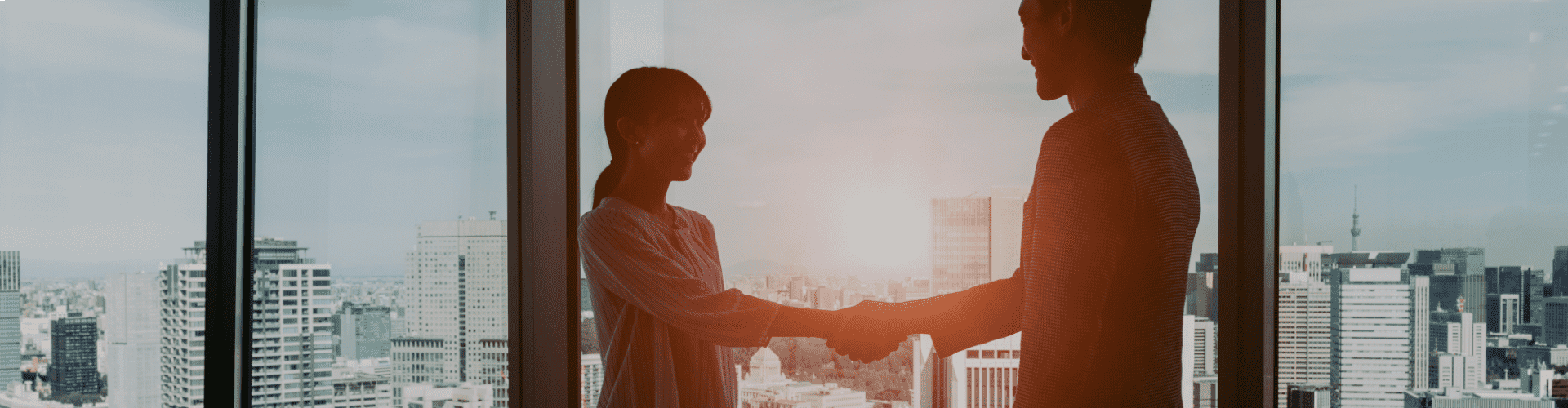
Problem Solving Examples
課題解決事例
お客様のお悩みを解決に導いた
東京パックのアイディアを一部ご紹介します。
Problem Solving Examples
お客様のお悩みを解決に導いた
東京パックのアイディアを一部ご紹介します。
シート状のプラスチックを片面だけの金型を使用して成型する所までは真空成型の成型方法と同じですが、シートを加熱して金型に密着させる時に真空しながら真空側と反対から圧縮空気を送りシートを空気圧を利用して金型に密着させる方法です。 真空成型よりも、より金型形状に忠実に表現でき、シャープな仕上がりになる為、商品価値を高めます。
当社の独自の成型技術で時間経過で反りが発生しないように製品を生産することに成功しました。
お客様からもご好評をいただきました。
シェルパックは通常 0.5mmPET が多いいですがワンウエイから容器として使用したいので材厚を1mmに変更したいとのご要望がありました。
しかしヒンジ部が割れてしまう事例があるため成型と筋押し(ミシン)を改良して折り曲げやすいヒンジを作ることができました。
当社の独自の成型技術を応用して厚物成形のヒンジにも応用ができました。
お客様からもご好評をいただきました。
1 mm~ 2 mm程の厚めの PP 材料の場合、通常の機構のヒンジでは思うように身と蓋を閉めることができず、別々の身と蓋にするしかないというご相談でした。
1 mm~ 2 mm程の厚めの PP 材料の大型シェルパックのヒンジを立体ヒンジに改良し独自の技術でトリミングを行うことで、長めのヒンジでも簡単に曲げることができるようになりました。
お客様からもご好評をいただきました。
比較的に環境配慮向けのバイオマス材料は、従来のプラスチック材料に比べて成型が難しいのが特長です。
特にマプカは紙が 51%のため通常の成形が形にならないことが多くありました。
当社独自の成型技術を確立させました。
その結果、バイオマス材料のトレイが次々に生産されています。
お客様からもご好評をいただきました。
従来のシェルパックの勘合では、開けやすさを重視すると開きやすくなって密閉性が悪くなり、中身を守るために開きにくい構造にするとシェルパックが開きにくいという矛盾した問題がありました。
外側にフック形状の機構を設計したことにより、開きやすさを重視した時に自然と開いてしまう問題点を解消し、開きにくくしたことにより開封しにくいという問題点を解消することが出来ました。
また、この機構にしたことによる勘合の密閉性は従来のシェルパックと遜色ありません。